AIR COMPRESSOR SKID PACKAGES
Containerized, turnkey systems for providing compressed air to businesses. Containerized modules containing process equipment are custom-built to the specified size and configuration. Designed to work in various climate zones.
CAPACITY
up to 300,000 m³/h
PRESSURE
up to 40 MPa
WARM UP PERIOD
up to 20 minutes
OPERATING TEMPERATURE
–50 to +40°C
The basic compressor skid package includes a compressor, drier, receiver, filters, a control system, and the plant's life support equipment. The facility functions automatically and does not require a permanent operator presence.
The discharge air from the compressor skid package satisfies the standards. The air pollution class will be determined by the application.
PRODUCT IMAGES
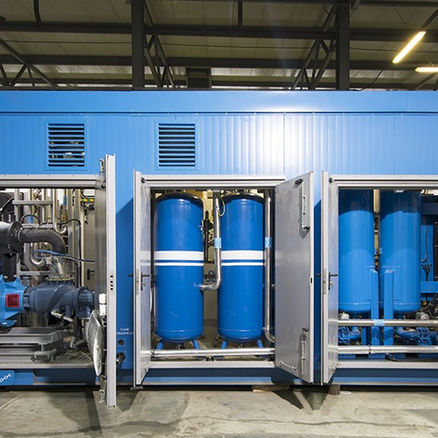


CONFIGRATION OF AIR COMPRESSOR SKID PACKAGE
Air purification and dehydration system
-
Ensures elimination of moisture, oil, and solids.
-
The air is treated in compliance with GOST R ISO 8573-1-2005 for compressed air. Contaminants and Purity Classes »
-
Air can be treated to meet any purity class (0–5).
Filtration systems
-
Coarse and fine filters (0.03-0.01 μm) and oil vapour filters
-
Carbon column (optional) assures compressed gas is nearly free of hydrocarbon vapours (< 0.003 mg/m3).
Dryer
-
Refrigerated type (dew point up to +3°C).
-
Adsorption type (dew point ranges from +3 to -70°C).
Compressor
-
Screw type (oil-injected and oil-free)
-
Reciprocating type (oil-injected and oil-free)
-
Centrifugal type (oil free)
-
Scroll type (oil-free).
Compressor
-
Screw type (oil-injected and oil-free)
-
Reciprocating type (oil-injected and oil-free)
-
Centrifugal type (oil free)
-
Scroll type (oil-free).
Booster compressor (optional).
Designed to boost the compressor's pre-compression pressure.
Containerized module.
-
All climate versions
-
All containerized module configurations (any size)
-
Explosion-proof variant (optional).
AIR COMPRESSOR SKID PACKAGE AUXILIARY EQUIPMENT
Plenum-and-exhaust ventilation system
We employ a recirculation ventilation system, which enables for:
-
Save up to 100 kWh of electricity for winter heating, disconnect from external heat sources, and ensure proper gas composition in the space.
-
Maintains an appropriate ambient temperature for the installed equipment.
Heating system
-
Heating sources include electricity and industrial hot water.
-
Security and fire alarms.
Outdoor and indoor emergency lighting
Includes regular lighting, emergency lighting, escape lighting, exterior lighting, and maintenance lighting.
LED lighting:
-
Energy-saving LED general and emergency lighting systems;
-
Emergency lighting runtime of at least 2 hours;
-
Outdoor lighting with IP54 or higher LED luminaires;
-
System for explosion protection of process equipment by applying overpressure inside the containerised module (optional)
PRODUCT DESIGN OPTIONS
Capacity: up to 300,000 m³/h
Pressure: up to 40MPa
Dew point temperature:−70°C
Operating temperature:−50 to +40°C
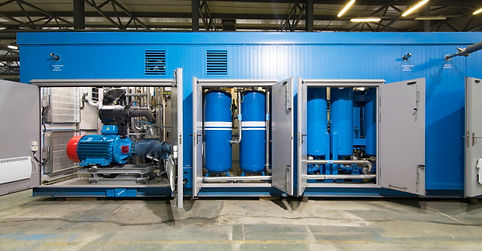
BENEFITS OF CONTANIRIZED MODULE
All climatic versions
U, UKhL, KhL, T, TS, TVM, OM, TM
All containerized module configurations (all sizes)
Explosion-proof version (optional)
Long-lasting anti-corrosion coating
-
3 coats of certified paint materials from leading Russian and foreign manufacturers; service life of the paint materials is up to 24 years.
-
Paint materials for the oil and gas sector: all climate zones, all types of atmospheres and placement categories.
-
In different climate zones, unprotected steel is exposed to corrosion, which leads to its destruction.
-
A durable paint coating must be used to protect the containerized module against corrosion.
Thermal insulation
-
We use three layers of environmentally friendly, non-combustible insulation up to 200 mm thick.
-
We insulate doors, walls, ventilation ducts, valve actuators, and external hatches of aegis projects technology skids, which allows the plant to start-up quickly by accelerating the heating of the equipment after downtime under the heating off conditions.
-
The lack of high quality and airtight thermal insulation of the containerized module and its components leads to high heat losses and therefore significant energy costs, as well as condensation which can cause equipment failure.
Stainless steel pipes in process piping ensure the absence of corrosion (hot, humid air under pressure leads to rapid corrosion of ferrous steel piping and damage to filters, process equipment, and instrumentation) and the long-term operation of the compressor plants.
Electrics
-
The use of reliable start-up automation from ABB, Schneider Electric ensures trouble-free start-up of all plant systems
LED lighting
-
Energy-saving LED general and emergency lighting systems
-
Emergency lighting runtime of at least 2 hours
-
Outdoor lighting with IP54 or higher LED luminaires
Aluminum flooring (no corrosion)
-
We use aluminum flooring to avoid corrosion.
-
Steel corrugated floors are made from hot-rolled sheet metal. Such a floor rusts quickly, because a rust spot appears in the sheet already at the production stage. For the same reason, painting a steel floor will not protect it from rust.
We use high-strength and durable galvanised and stainless-steel cable trays
Sophisticated thermal insulation of the containerised module
-
We insulate doors, walls, ventilation ducts, valve actuators, and external hatches, which allows the plant to start-up quickly by accelerating the heating of the equipment after downtime under the heating off conditions.
-
Insulation and sealing of the piping outlet recesses protect the plant from moisture and dust ingress and heat loss.
Convenience for Design Organizations
We provide a complete package of design and detailed engineering documentation: process and schematic diagrams, all necessary calculations
Ongoing technical support and professional advice throughout the project
Ease of Use
-
The design of the containerized modules allows easy access for plant maintenance (equipped with a swing gate, sufficiently wide passages to work in)
-
The design of modular compressor plants is based on the principle of minimizing the need for human intervention in the operation of the plant. No permanent staff presence is required
-
The equipment requires a minimum of maintenance (standard maintenance as recommended by the manufacturers of the core process equipment)