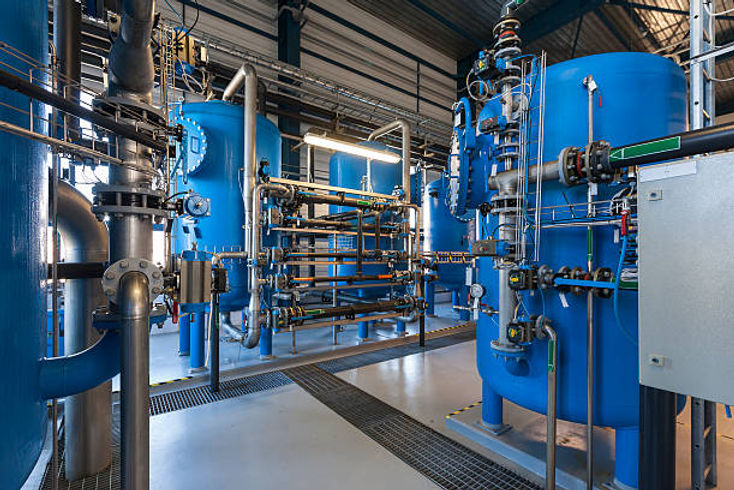
FILTERATION
PROJECTS
Aegis Projects Technology is a well-known manufacturer, supplier, provider, and fabricator in India. They are one of the leading businesses in the Magnetic Separator, Magnetic Coolant Filter, Magnetic Coolant Filtration System, Rare Earth Magnetic Separator, Rare Earth Magnetic Coolant Filter, Cyclone Filtration System, Cyclone Filter, Cyclone Coolant Filtration System, Coolant Filtration System, Compact Band Filter, Compact Band Coolant Filter, Sludge.
SYSTEM FOR CYCLONE FILTERATION
Aegis projects technology Cyclone filter systems are made to filter both ferrous and nonferrous materials. A pressure pump is used to generate super centrifugal force inside the conical housing.
Using vertex separation, cyclone filtering is a technique for eliminating particles from liquid without the need for filter material. To separate solid from liquid, gravity and the rotational effect are employed. A high-speed rotating flow is established within a conical container known as a cyclone. Liquid flows in a helical pattern, starting from the top broad end and finishing at the bottom narrow end. Before the top of the cyclone, a straight liquid flows through the sides of the cyclone, and liquid and clean liquid emerge from the top. Solid particles rotate with the liquid due to the super centrifugal force around the outer wall; solid particles fall to the bottom of the cyclone due to gravity and rotational force and are eliminated.
FACILITY:
-
Coolant Tank.
-
Cyclone (filter)
-
Equipment includes a gravity sludge separator, chiller, heat exchanger, and supply pump (delivery pump).
-
Pumps for scrubbing, bed flushing, and transfer.
-
Cyclone Pump
-
Features include a magnetic separator, oil skimmer, level indicator, and automatic control panel.
-
Wheel cleaning pump
-
Chiller Pump
BENEFITS:
-
No filter medium is required.
-
Clean tank cleaning is not necessary.
-
Increase the life of your wheels and tools.
-
Superior Surface Finish and Quality
-
Faster operation, optimum cycle time, and increased productivity.
-
Superior life and performance of tool and cooling lubricants
-
Superior process reliability.
-
Environment and Health Safe Working
-
Minimum space use on the shop floor.
-
Help to attain proper R.A. (roughness average) Value.
-
Maintain the RA and RZ values.
FEATURES:
-
Cyclone pump
-
Gravity sludge separator
-
Automatic control panel
-
Inspection nozzle for clean coolant
-
Cyclone system with landis granding m/c
-
Cyclone system with copper wire drawing m/c with stand alone chiller
-
Cyclone system with landis m/c with deep in type chiller
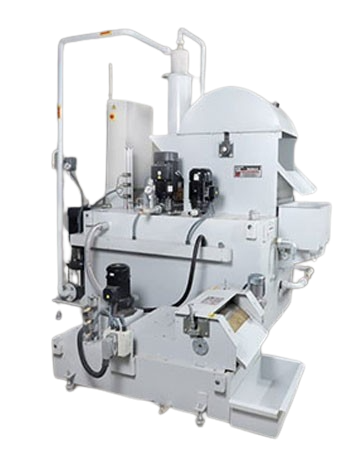
SLUDGE MASTER
sludge master filter is designed to filter ferrous and non-ferrous solid particles from liquid with high degree of purification using paper as filter media to enhance life of liquid and protect surface finish of products. Sludge master works both with water base and oil base (neat oil). Sludge master’s material of construction is mild steel, SS-304 and SS-316
FACILITY:
-
include a cooling tank and a sludge master filter.
-
Chiller, heat exchanger, and supply pump (delivery pump).
-
Scrubbing Pump
-
Bed Flushing Pump
-
Transfer Pump
-
Magnetic Separator Oil Skimmer Level Indicator
-
Automatic Control Panel
-
Wheel cleaning pump
-
Chiller Pump
BENEFITS:
-
Superior Surface Finish and Quality
-
Faster operation, optimum cycle time, and increased productivity.
-
Superior life and performance of tool and cooling lubricants
-
Superior process reliability.
-
Environment and Health Safe Working
-
Minimum space use on the shop floor.
-
Help to attain proper R.A. (roughness average) Value.
-
Maintain the RA and RZ values.
FEATURES:
-
Easy cleaning system for tank with wheels
-
Hinge on front top body

PAPER BAND FILTER
The Aegis Projects Technology Paper Band Filter is a gravity filter that continuously cleans itself. Solids are removed as liquid passes through the filter media before being dumped into a garbage in a reasonably dry state. The filter media is transported by an unending conveyor. The conveyor's sloping sides form a deep pool for the liquid, and an inclined discharge ramp transports the garbage. Aegis projects technology Paper Band Filters are offered in carbon and stainless steel to fulfill the majority of process requirements. Stainless variants are perfect for all food processing applications. They adhere to FDA criteria, can handle corrosion-resistant applications, and give enhanced longevity in acidic situations. Custom units are available in a variety of configurations to fulfill even the most demanding applications.
FACILITY:
-
Include a cooling tank and a sludge master filter.
-
Chiller, heat exchanger, and supply pump (delivery pump).
-
Scrubbing Pump
-
Bed Flushing Pump
-
Transfer Pump
-
Magnetic Separator Oil Skimmer Level Indicator
-
Automatic Control Panel
-
Wheel cleaning pump
-
Chiller Pump
BENEFITS:
-
Superior Surface Finish and Quality
-
Faster operation, optimum cycle time, and increased productivity.
-
Superior life and performance of tool and cooling lubricants
-
Superior process reliability.
-
Contribute to achieving the right R.A. (roughness average) value.
-
Maintain the RA and RZ values.

SMART MAG
Smart Mag Coolant Filter is designed to filter ferrous solid particles using a magnetic drum.
The unclean coolant from the machine enters the magnetic filter's inlet, passes between the magnetic roller and the body gap, and the magnetic drum collects dust. A rubber roller mounted atop a magnetic roller with a spring tension system. The rubber roller crushes the damp dust, leaving only dry powder in the garbage. Smart Mag is compatible with both water and oil-based coolants (neat oil). Smart mag MOC is made of both mild and stainless steel.
APPLICATION:
-
Water-based coolant.
-
Grinding machine
-
Chip separator
-
Wire Drawing Machine
-
Induction heating
-
Stainless steel 420 grade motor shaft
-
Cold Rolling Mill
-
Fine Boaring.
-
Cast Iron Dust Separator
-
Oil-based coolant.
-
Shaving process
-
Gear grinding
-
Tooth grinding
-
Honing machine
BENEFITS:
-
Metal is eliminated in the primary step.
-
Remove floating and settling dust.
-
Smart Mag reduces the amount of media consumed through filters.
-
Increases coolant life.
-
Increases the life of wheels and tools.
-
Reduced tank cleaning frequency
-
Maintains the RA value.

OIL SKIMMERS
Aegis Projects Technology Engineers create and produce many types of oil skimmers to remove excess oil and undesirable high viscous liquids that float on the surface of useful liquids such as grease oil or alkaline base liquid on water.
FACILITY:
-
Include a floating gravity oil skimmer and a tube oil skimmer.
-
Disk oil skimmer
-
Stainless steel hinge belt oil skimmer.
-
Stainless belt oil skimmer
-
PU belt oil skimmer.
-
Polymer belt oil skimmer.

CENTRALIZED FILTRATION SYSTEM
A centralized filtration system is essentially a shared filtration system for a set of equipment. Thus, a centralized filtering system may serve the entire shop.
Aegis Projects Technology Engineers is a major manufacturer of centralised cyclone coolant filtering systems. Cyclone filtration systems are meant to filter ferrous and non-ferrous solid particles from liquid/coolant. For fine filtration, a pressure pump generates super centrifugal force in a conical container. We can filter both water and oil-based coolants (neat oil).
For neat oil, first filtration is performed using Smart Mag, which filters the largest number of dust particles. After that, the coolant enters a cyclone filtration system, where we obtain roughly 30 to 20 microns of filtration. The filtration level is determined by the viscosity of the oil. A specific bag is utilized for fine filtration, which can achieve filtration levels as low as 1 micron.
For water-based coolant, primary filtering is done with Smart Mag, and then the coolant enters the cyclone, where we get around 10 microns of filtration, which is appropriate for water-based coolant applications.
The cyclone coolant filtering system is totally automatic and does not require any filter media. The drain is connected to a gravity sludge separator; ferrous dust particles are attracted by magnets, while non-ferrous particles settle by gravity, and dust exits through a scraper bled.
Aegis Projects Technology creates coolant tanks that contain no floating or settled dust particles. Coolant tank is separated into two parts: clean and semi-clean. High-density and low-density dust constantly move from the clean tank to the semi-clean tank. Hence, we do not get dust in clean tank.
FACILITY:
-
Coolant Tank.
-
Cyclone(filter)
-
Equipment includes a gravity sludge separator, a chiller with heat exchanger, and a chiller pump.
-
Scrubbing Pump
-
Bed Flushing Pump
-
Wheel cleaning pump
-
Automatic Control Panel
-
Cyclone Pump Delivery Pump
-
Transfer Pump
-
Magnetic Separator Level Indicator
BENEFITS:
-
No need for filter media.
-
Clean tank cleaning is not necessary.
-
Increase the life of your wheels and tools.
-
Tank cleaning frequency is lower than others.
-
Superior Surface Finish and Quality
-
Faster operation - optimum. Cycle time - increased productivity
-
Superior life and performance of tool and cooling lubricants
-
Superior process reliability.
-
Environment and Health Safe Working
-
Minimum space use on the shop floor.
-
Contribute to achieving the right R.A. (roughness average) value.
-
Maintain the RA and RZ values
FILTER HOUSING
Aegis Projects Technology Engineers construct filter housings for filter bags, cartridges, and baskets to filter water, oil, chemicals, acids, and pharmaceuticals, providing filter ranges from coarse to fine filtrations.
Aegis Projects Technology Engineers manufactures a comprehensive selection of Bag Filter Housing to fulfill your liquid filtering requirements. Our bag Filter housings are designed to be ideal for liquid filtration in a variety of sectors. We manufacture single bag, multi bag, and duplex filter housings. We manufacture filter housings in mild steel, SS-304, SS-304L, SS-316, and SS-316L.
FACILITY:
-
include bag filter housing.
-
Cartridge filter housing.
-
Basket filter housing.
-
Multibag housing.
-
Bag. Cartridge.
-
Basket.
-
Three-way valve.
-
Pressure gauge
-
Differential Pressure Switch
-
I-bolt, I-nut
-
O ring fittings
BAG DIMENSIONS
-
include 7" x 32", 7" x 20", and 7" x 16".
-
filtering ranges from 1000 to 0.5 microns, with cartridge and basket options available depending on the application and filtering level.
BENEFITS:
-
Faster operation, optimum cycle time, and increased productivity.
-
Quality consistency.
-
Superior process reliability.
-
Environment and Health Safe Working
-
Minimum space use on the shop floor.
-
Easy to clean from the inside.

FILTER HONING MACHINE
ULTRA OIL FILTERS
Aegis projects technology engineers create ultra oil filters for honing, lapping, and super finishing applications. The primary filtration is done by a powerful back earth magnetic separator. The unclean oil from the machine enters the entrance of the magnetic filter, coolant flows between the magnetic roller and the body gap, dust is captured by the magnetic drum, and semi-clean liquid falls into the semi-clean tank. The semi-clean liquid is sent to the Ultra oil filter via a transfer pump. Semi-clean liquid goes through a specific bag to attain the necessary filtration level. Filtration of up to one micron is possible.
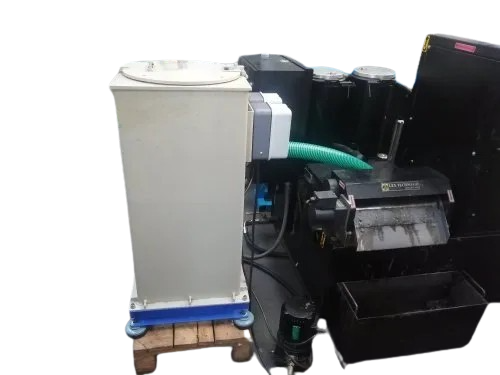
SLUDGE MASTER
Aegis projects technology engineers create sludge masters for honing, lapping, and superfinishing applications. The primary filtration is done by a powerful back earth magnetic separator. The unclean oil from the machine enters the entrance of the magnetic filter, coolant flows between the magnetic roller and the body gap, dust is captured by the magnetic drum, and semi-clean liquid falls into the semi-clean tank. The semi-clean liquid is transferred to the sludge master via the transfer pump. Semi-clean liquid goes through filter paper. Filtration can reach up to 10 microns.

GRAVITY FILTER
Aegis Projects Technology Engineers create Gravity Filters for Honing, Lapping, and Superfinishing applications. The primary filtration is done by a powerful back earth magnetic separator. The unclean oil from the machine enters the entrance of the magnetic filter, coolant flows between the magnetic roller and the body gap, dust is captured by the magnetic drum, and semi-clean liquid falls into the semi-clean tank. The semi-clean liquid is sent to the gravity filter via the transfer pump. Semi-clean liquid goes through filter paper. Filtration up to 20 microns can be accomplished.

FACILITY:
-
Coolant tank Sludge master (filter)
-
Ultra-oil Filter
-
Equipment includes a gravity filter, a heat exchanger, a chiller pump, a supply pump, and a transfer pump.
-
Magnetic Separator Level Indicator
APPLICATION:
-
Shaving procedure.
-
Gear grinding
-
Tooth grinding
-
Honing machine
-
Super Finishing Machine
-
Grinding machine
-
The Lapping Machine
BENEFITS:
-
Superior Surface Finish and Quality
-
Faster operation, optimum cycle time, and increased productivity.
-
Superior life and performance of tool and cooling lubricants
-
Superior process reliability.
-
Environment and Health Safe Working
-
Minimum space use on the shop floor.
-
Contribute to achieving the right R.A. (roughness average) value.
-
Maintain the RA and RZ values.
ROTARY SELF CLEANING FILTER
Aegis projects technology engineers created a rotary self-cleaning filter to separate solid particles from liquid using a certain grade of mesh. URSF operates entirely on autopilot, requiring no manual intervention.
The machine outlet is linked to the URSF intake, the liquid travels through an appropriate mesh, and the desired filtering is obtained. The chip particles land on the rotary blade and are cleaned by air pressure; the dust produced is collected in a trash.
APPLICATION:
-
Industrial component washing machine.
-
Pilling Machine
-
Gun drill machine
-
Deep hole drilling machine
-
CNC Drilling Machine
-
VMC HMC
-
Gear hobbing machine.
-
This system is appropriate for water-based and oil-based liquids or coolants.
BENEFITS:
-
Metal is eliminated in the primary step.
-
Remove floating and settling dust.
-
The use of URSF reduces the usage of filter media.
-
Increases coolant life.
-
Increases the life of wheels and tools.
-
Reduced tank cleaning frequency
-
Process reliability
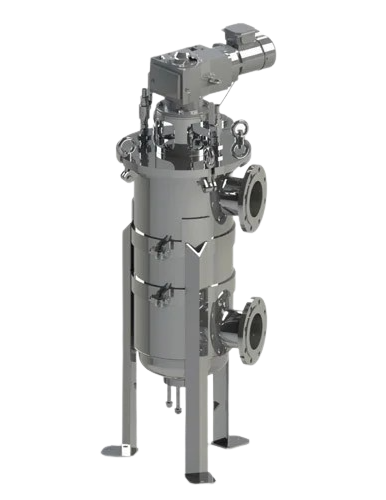
FILTER MEDIA AND SPARE PARTS
Aegis Projects Technology Engineers provides nonwoven filter media, often known as filter paper, for usage in a number of applications and industries. Coolant filter paper rolls are commonly used to filter oils, water, and coolants. Liquid passing through that type of medium receives appropriate filtration.
FUME AND DUST CLEANER
"Fume cleaner" is a phrase commonly used to describe a fume extraction or fume filtration system found in laser cutting equipment. These systems are intended to remove or filter the fumes, smoke, and other airborne particles produced during the laser cutting process.
Overall, fume cleaner systems are critical to maintaining a safe and healthy work environment by lowering the danger of exposure to toxic fumes and particulates produced during laser cutting operations.
Facilities include fume capture, filtration, and customizable options.
Features include automatic cleaning, noise reduction, compact design, and ease of maintenance.
WORKING:
Aegis Projects Technology's fume and dust cleaning effectively removes particles from welding, soldering, laser cutting, and chemical processes.
When fumes and dust pass through the fume chamber's inlet at the same time, sprinkles of water are dropped into the chamber from above. Once the impurities are dissolved in the water, it enters a filtration system where it is filtered through filter paper and solid particles exit through the paper.
This procedure might help to clean up your industry by filtering out toxic gases and odors. It will be useful for both nature and the workers in the company.
BENEFITS:
-
Improved Air Quality: FumeCleaner effectively removes toxic fumes and particles produced during the laser cutting process, resulting in a cleaner and safer working environment.
-
Health and Safety: By limiting exposure to dangerous emissions, FumeCleaner protects the health of machine operators and other staff working near laser cutting machines.
-
Compliance: FumeCleaner assists businesses in meeting health and safety standards governing air quality and emissions, lowering the risk of fines and penalties.
-
Enhanced Productivity: Cleaner air creates a more comfortable and productive work environment for machine operators, potentially increasing efficiency and production.
-
Cost Savings: The FumeCleaner's efficient filtering system reduces the need for costly repair and replacement of machine components damaged by fume buildup.
