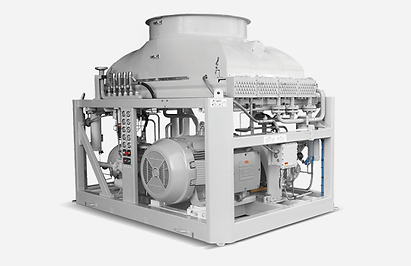
COMPRESSOR UNITS
CNG stations use reciprocating compressor machines with a wide range of pressure and capacity. The compressor unit is responsible for natural gas compression.
OPERATING FLOW RATE
up to 4,800 m³/h
OPERATING PRESSURE
up to 7.5 MPa
COMPRESSION STAGES
2 / 3 / 4 / 5
TRANSMISSION
direct/belt
The compressor unit includes the following equipment:
-
A frame-mounted compressor powered by a direct drive or belt-driven electric motor, with air or water-cooled cylinders;
-
The gas air cooling unit
-
Safety interstage valves.
-
Interstage moisture and oil separators.
-
Compressor unloading system.
-
Oil system and gas lines.
-
Automation sensors, instruments, and electrical equipment.

GAS DRYING UNIT(AT THE INLET)
Designed for gas purification and adsorption drying at the compressor's input. The gas drying device is intended for use with low-pressure gas pipelines. This device is designed to run in two cycles: dehydration and regeneration. It can be delivered in a container upon request.
THROUGHOUT CAPACITY
up to 3,000 m³/h
PRESSURE IN ADSORBER
up to 1.6 MPa
OUTLET MOISTURE CONTENT
up to 0.009 g/m³

GAS DRYING UNIT(AT THE OUTLET)
Designed to minimize moisture content in high-pressure compressed natural gas traveling through it while also purifying CNG from mechanical contaminants. This inhibits the production of crystalline hydrates in pipelines while refueling various road vehicles.
THROUGHOUT CAPACITY
up to 3,000 m³/h
PRESSURE IN ADSORBER
up to 24.5 MPa
OUTLET MOISTURE CONTENT
up to 0.009 g/m³
The gas drying equipment is situated near the compressor outlet. The unit can be equipped with a moisture meter that sends data to the control room console. The unit is regulated automatically.

CNG STORAGE SYSTEM
The CNG Storage System is intended to store compressed natural gas (methane), quickly refuel natural gas vehicles, and reduce the number of compressor unit starts. The system is a cassette assembly of high-pressure cylinders.
CYLINDER CAPACITY
80 to 400 L
OPERATING PRESSURE
up to 24.5 MPa
NUMBER OF LINES
1 / 2 / 3
VALVE ACCTUATOR
electrically driven
The CNG Storage System is offered in single, dual, and triple line configurations with a priority panel. The system's entire capacity is tailored to the needs of each customer. It can be sent in a vented container to protect the equipment from precipitation.

CNG DISPENSERS
CNG dispensers are designed to fill cylinders of motor vehicle fuel systems, mobile gas refuellers and cassette assemblies with compressed natural gas, to meter the volume of gas dispensed, normalised to standard conditions, and to calculate the cost of the dose dispensed.
CAPACITY
up to 70 m³/min
NUMBER OF DISPENSING HOSES
2 / 3
NUMBER OF LINES
1 / 2 / 3
OPERATING TEMPERATURE
−40 to +40 °Ð¡
Available in one, two, and three stage dispensers, each with one or two dispensing hoses. The twin-hose dispensers feature two separate measuring channels. The major benefits of this technology include cutting-edge technology, appealing design, strong construction, and low-cost service.
CNG dispensers are supplied in the following configuration:
-
Stainless steel frame constructed to international standards;
-
Mass flow meters and cut-off clutches.
-
Manually deactivate the refueling;
-
The computerized display of each refueling hose shows the price, the volume filled, and the total amount in the currency of your choice.
-
Pressure gauge.
-
Each station includes two pressure sensors, an emergency stop button, an explosion-proof version, and input filters.
-
The capacity to share data with the custodial metering system.

INTAKE VALVE MODULES
The intake valve skid is intended to deliver and automatically turn off gas to the compressor unit, with discharge to the gas flare. A custody transfer meter is an optional feature for the system.
OPERATING FLOW RATE
up to 5,000 m³/h
OPERATING PRESSURE
up to 10 MPa
NOZZLE DIAMETER
50 / 80 / 100 / 150 mm
The CNG station's automation system controls the discharge and shut-off valves. The inlet valve skid is equipped with an emergency manual pushbutton. The inlet valve skid is designed to operate at temperatures ranging from -40 to 45 degrees Celsius.
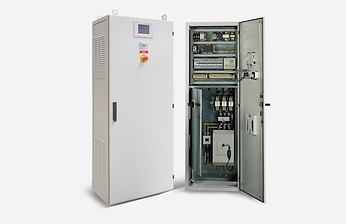
AUTOMATIC CONTROL SYSTEM (COMPRESSOR UNIT)
The Automatic operate System (ACS) is used to operate the compressor unit using a predetermined algorithm, monitor parameters, protect the compressor unit from emergency operating situations, provide information on the status of machinery, and communicate the unit status to a higher level.
The compressor unit ACS provides:
-
Remote start-up and shutdown of the compressor unit.
-
Measurement of gas pressure and temperature at the compressor's input and outlet
-
Monitoring the pressure of the lubrication system.
-
If a fire is detected, the compressor unit should be shut down immediately.
-
Automatic gas pressure control at the outlet.
-
Drive motor start-up lock and shut-down in case of emergency or if compressor unit process parameters do not match the established values.
-
Functional communication with the superordinate ACS (using an established protocol);
-
Operating parameters for the compressor unit are being archived.

AUTOMATIC CONTROL SYSTEM (CNG STATION)
The automatic control system (ACS) is an information and control system that monitors and controls all of the CNG station's process equipment and auxiliary mechanisms. The ACS is used to regulate the compressor unit using a predetermined algorithm, monitor parameters, protect the compressor unit from emergency operating situations, provide information on machinery status, and communicate unit status to a higher level.
The compressor units are equipped with a programmable controller-based automation system that provides:
-
Remote start-up and shutdown of the compressor;
-
Measurement of gas pressure and temperature at the compressor's input and outlet
-
Monitoring oil pressure and temperature in the lubrication system;
-
If a fire is detected, the compressor unit should be shut down immediately.
-
Automatic gas pressure control at the outlet.
-
Maintaining the appropriate temperature in the container.
-
Motor start-up lock and shut-down in case of emergency or if compressor unit process parameters do not match the established values.
-
Functional communication with the superordinate ACS (using an established protocol);
-
Archiving the compressor unit's operating parameters;
-
Functional communication with the superordinate ACS (using an agreed-upon protocol).
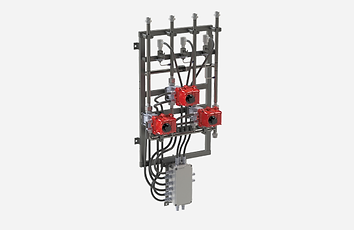
PRIORITY PANEL
The priority panel is intended to manage the sequence of filling sections of the gas-charged accumulator unit in a specific order, with subsequent gas supply to CNG dispensers. It is controlled by the CNG station's automatic control system.
NUMBER OF LINES
1 / 2 / 3
DRIVE
electrically driven

MODULAR CONTAINER
The modular container is intended to shield the process equipment from precipitation while also allowing it to operate at low ambient temperatures.
The containerized module houses the core process equipment:
The system includes a compressor, gas treatment unit (dryer), priority panel, CNG storage system, automatic control system (optional), intake valves module, and CNG dispensers.
The modular container is outfitted with heating, lighting, ventilation, gas control, fire alarm and automatic fire extinguishing systems, as well as audio and light alerts. The containerized modules are designed to fit any site and may be erected quickly.