HEAT EXCHANGERS
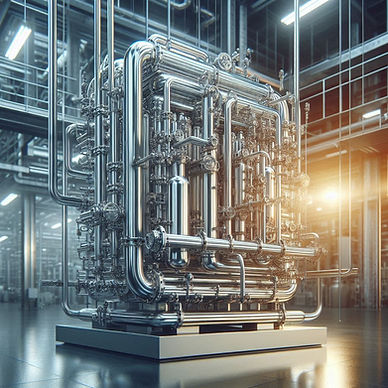
PLATE TYPE
HEAT EXCHANGER
Plate type heat exchangers (PHEs) employ a series of thin plates to transfer heat between two fluids. They are widely employed in a variety of industries, including chemical, petroleum, HVAC, refrigeration, dairy, pharmaceutical, beverage, liquid food, and health care.
​
The primary components of a plate heat exchanger are:
-
Plates: Thin, rectangular metal plates, such as stainless steel or titanium, layered together to form a heat exchanger.
-
Gaskets: Sealing gaskets located between the plates to direct fluid flow and prevent leaks.
-
A frame connects the plates and provides structural support.
A plate heat exchanger works on the idea of heat transfer by conduction and convection. Hot and cold fluids pass through the channels between the plates, while heat is conveyed between the plates and gaskets.
​
Plate heat exchangers are classified into numerous categories, which include:
-
Gasketed plate heat exchangers are the most popular type, with the plates sealed with gaskets to prevent leaks.
-
Brazed plate heat exchangers employ a brazing method to seal the plates together.
-
Welded plate heat exchangers employ a welding procedure to seal the plates together.
-
Semi-welded plate heat exchangers combine gasketed and welded plates.
Plate heat exchangers have several advantages, including:
-
High heat transfer efficiency.
-
Compact design.
-
Low pressure decrease.
-
Easy to maintain and clean.
-
Wide range of applications​
​
Plate heat exchangers are widely used in various industries, including:
-
Chemical Processing
-
Petroleum Refining
-
HVAC systems
-
Refrigeration Systems
-
Dairy Processing
-
Pharmaceutical manufacturing
-
beverage processing
-
Liquid food processing
-
Healthcare applications
APPLICATIONS
Constantly producing more with less energy, material, and space
With compact and flexible heat exchanger design, we are dedicated to bringing efficiency, dependability, cost-effectiveness, and ease of maintenance to systems used in a wide range of industries, resulting in desired thermal performance and economic values from less energy, material, and space.
HEAT RECOVERY
Smarter ways to recover and reuse heat.
Energy prices will continue to climb, while sectors around the world face increasingly rigorous requirements for reducing CO2 emissions. Today, global industry consumes enormous amounts of energy, and the most concerning aspect is that up to half of it is wasted owing to inefficiency and complexity in the recovery of low-grade energy. Heat in the form of vapor, hot water, or hot air is produced during practically every industrial cycle, but it does not have to be wasted. With intelligent systems, it can be recovered and repurposed for other purposes, contributing to a reduction in carbon emissions and significant cost savings for both producers and end users.
Brazed plate heat exchangers provide effective heat recovery.
So far, gasketed heat exchangers have been the dominant heat recovery technology, requiring a large amount of space and regular maintenance. Brazed plate heat exchangers provide the same power but are far more compact and almost maintenance-free. Our plate heat exchanger allows for efficient heat recovery in a variety of applications:
Air Compressors Co-Gen and Gen-Set ORC Process Industry
​
BOILERS
Optimal heat transfer and compactness
Our E-type brazed plate heat exchangers are designed for high-efficiency water-to-water heat transfer in systems with low pressures and mild temperatures. They are developed to fulfill your individual requirements for large-scale gas boiler manufacturing by providing optimal heat transmission and compactness for both condensing and non-condensing boilers.
Our E-type is the most efficient brazed plate heat exchanger available today, with nearly all of the material contributing to heat transmission. The unit can be outfitted with connections for various pipe fittings or stud bolts for mounting on a hydraulic block

AMMONIA SYSTEMS
Ammonia can be used as a refrigerant in many industrial and commercial refrigeration systems, including:
-
Cold storage
-
The food and beverage sector includes chemical and process factories.
-
Ice rinks
-
Commercial Refrigeration Systems
-
Commercial and industrial heat pumps
-
Ammonia, R717, is an appealing refrigerant option with a wide application range from high to low temperatures and a significantly lower cost (per kg) than HFC refrigerants.
Heat exchanger functions in ammonia systems can operate as follows:
-
Evaporator: Direct expansion.
-
Flooded
-
Thermosyphon
-
Pumped circulation
-
Condenser
-
Equipment includes a desuperheater, economizer, cascade, compressor, and oil cooler.
-
Thermosyphon is MEG cooled.
-
Water chilled.
CHILLERS
Absorption refrigeration cycle.
To power the refrigeration cycle, an absorption chiller generates energy from a heat source. Our brazed plate heat exchangers provide for tight temperature approaches on low- and/or high-temperature streams, hence improving system performance.
-
MEG cooled
-
Water chilled.
​
Absorption heat pumps offer an additional method of generating heat.
Absorption systems are mostly employed in big absorption chillers. Smaller systems aimed at heating buildings, known as absorption heat pumps or gas-fired heat pumps, are becoming increasingly popular. When power is scarce or heat is abundant, absorption heat pumps offer an alternative method of generating heat. They may run on any heat source, including solar energy and geothermal hot water, among others. Absorption heat pumps are more energy efficient than gas boilers and can take use of low-quality ambient heat. They can be significantly more efficient by including brazed plate heat exchangers as intermediary single-phase heat exchangers. Our brazed plate heat exchangers provide highly efficient heat transfer, thereby reducing the heat input needed to achieve a particular effect.
​
Vapor compression cycle
A vapor-compression cycle requires the use of both an evaporator and a condenser. Highly efficient evaporators and condensers with specific refrigerant ranges for R410A, R32, R454b, R290, R134a, R1234ze(E), and R515b. These ranges have undergone extensive testing and verification in our in-house laboratory.
In addition to evaporators and condensers, we provide a variety of alternative heat exchanger solutions for vapor-compression chillers:
-
Economizers
-
Heat Recovery (De-Superheaters)
-
Internal heat exchangers
-
Oil coolers
-
Sub-coolers
AIR DRYERS
Prevent humidity and equipment damage.
Moisture condensation is a common issue in compressed air systems. In a typical system, the compressor draws in humid air and compresses it, raising its temperature. Cooling the air condenses water vapor cooled along the pipes, and then expanded water droplets form, causing corrosion, washing away lubrication oil, freezing when exposed to cold, and causing significant damage to the equipment that uses the air.
Integrated separator with a modular design.
To prevent water condensation in a pneumatic system, an air dryer can be placed to cool the compressed air to a temperature above the freezing point of water (down to 3 °C), causing moisture in the air to condense. The condensed liquid is removed from the system using separators.
Our innovative Air Dryer with Integrated Separator (ADWIS) units and dual-over-two-pass (D2P) combinations is a great solution for air dryers.
Heat transfer between refrigerant and air
ADWIS combines an efficient separator, a refrigerant-to-air heat exchanger, and an air-to-air heat recovery unit in a modular design that maximizes drying efficiency and performance. This inexpensive system provides consistent pressure decreases, easy drainage, and straightforward installation.
AIR COMPRESSORS
Keeping outlet temperatures at an all-time low
Air is heated anytime it is compressed, and it can easily reach 100°C in an oil-lubricated compressor and 200°C in an oil-free compressor. The use of compact brazed plate heat exchanger technology reduces the outlet temperature to the optimal working temperature in oil-lubricated screw compressors.
Temperature and corrosion control.
Oil lubricates and cools the working parts of screw compressors, as well as the air. SWEP brazed plate heat exchangers are utilized in oil coolers, air coolers, and heat recovery systems. Our copper-brazed units are suited for all oil types and can operate at temperatures up to 95 °C, while our stainless-steel units are ideal for use in harsh settings where oil contamination by copper at high temperatures must be avoided and maintenance kept to a minimum.
​
Suitable for all oil types.
SWEP heat exchangers are commonly utilized in oil/air coolers and heat recovery systems.
Our copper-brazed units, including the B60, B30, and B35T, are suited for all oil types running at temperatures up to 95 °C, as are our 100% stainless steel units.
OIL COOLERS
Custom brazed plate heat exchangers
Our modular and diverse product selection allows us to customize brazed plate heat exchangers for a variety of oil cooling applications.
Brazed plate heat exchangers provide several distinct benefits over shell and tube technology, which has been the dominating technology for oil applications.
Our heat exchangers are compact, have great thermal efficiency, and are easy to pick. They can handle a wide range of problems, including extremely viscous transmission oil and copper-free alternatives.
​
PROCESS INDUSTRY
Minimal maintenance and long equipment lifespan
In production environments with constant high volumes and automated processing around the clock, strong and compact heat exchangers are required to provide outstanding operational performance, low maintenance, and a long lifespan. Our heat exchangers excel at these crucial properties.
Customized design solutions for any need.
In addition to the strength and compactness of our heat exchangers, we will provide flexible and customizable design solutions for both plates and brazing materials to meet the specific requirements.
​